Corrosión
Cuando los Aceros Inoxidables sufren corrosión, generalmente no es uniforme como en el caso de los aceros al carbono, sino localizada. Debido a ello no puede prevenirse con espesores adicionales, sino que debe evitarse la corrosión misma por medio de un conocimiento profundo del medio corrosivo y del acero utilizado. Los aceros inoxidables no son atacados por el ácido nítrico u otros ácidos oxidantes, que facilitan la formación de la película protectora. Por otra parte, en general, estos aceros no resisten la presencia de ácidos reductores como el ácido clorhídrico o fluorhídrico, y son atacados por las sales de ellos (cloruros, fluoruros, bromuros y yoduros).
CORROSIÓN GENERALIZADA
Se debe al debilitamiento uniforme del film de pasivación (óxido de cromo) sobre toda la superficie del acero. Generalmente ocurre a causa de la mala selección del tipo de acero inoxidable. Un ejemplo de corrosión generalizada es exponer un acero inoxidable de tipo ferrítico de bajo contenido de cromo (AISI 430) a una moderada solución de ácido sulfúrico a temperatura. Se caracteriza por la presencia
de herrumbre en el acero. La vida de componentes se puede estimar en base a los resultados de pruebas de inmersión. Algunos métodos usados para prevenir o reducir la corrosión general son: recubrimientos, inhibidores, y protección catódica.
CORROSIÓN INTERGRANULAR
Este tipo de corrosión ataca generalmente a los aceros del tipo 18/8 (serie 300), que se expone
a temperaturas entre 430 a 870°C, estas temperaturas se presentan en las proximidades de
las zonas soldadas. Se forman carburos de cromo en los límites de los cristales de Austenita, empobreciendo la zona adyacente de este elemento (cromo) y quedando de esta forma expuesto a la corrosión. Una forma de evitar la corrosión intergranular es usar aceros de bajo contenido de carbono (tipo L), y cuando las condiciones de temperatura son aún más severas se debe usar aceros estabilizados. tipo de corrosión y reducir la agresividad del ambiente.
CORROSIÓN POR PICADURAS (PITTING)
Las picaduras son una forma localizada de ataque corrosivo. Se caracteriza por la formación
de agujeros en el metal. Estos agujeros pueden ser pequeños y difíciles de detectar visualmente
debido a la corrosión general. El pitting se asocia con discontinuidades localizadas del film de pasivación. La sensibilidad al pitting aumenta con condiciones extremas de agentes corrosivos, imperfecciones mecánicas, tales como partículas extrañas, daño en la superficie del material, o por fallas en la película de óxido de cromo. El fenómeno ocurre cuando se rompe la capa pasivante y hay un ataque muy localizado. Algunos métodos para reducir los efectos de la corrosión por picaduras
son: reducir la agresividad del ambiente y utilizar materiales resistentes a las picaduras. Es posible prevenir o retardar este efecto, usando aceros con contenido de Molibdeno, como el 316.
CORROSIÓN GALVÁNICA
CORROSIÓN BAJO TENSIÓN
(STRESS CORROSIÓN CRACKING, SCC)
La corrosión bajo tensiones corresponde a una falla de material, la cual es originada por la presencia simultánea de un ambiente adecuado, un material susceptible, y la presencia de tensiones. La temperatura es un factor ambiental significativo que afecta el agrietamiento. La tensión umbral está frecuentemente por debajo del punto de fluencia del material. Una falla catastrófica puede ocurrir
sin deformación significativa o el deterioro visible del componente. La soldadura genera gradientes de temperatura y así puede inducir tensiones residuales, lo cual en ciertos ambientes puede resultar en rotura por corrosión bajo tensiones. Este tipo de corrosión es el menos frecuente, se trata de un tipo de corrosión transgranular, el cual es producido por tensiones generadas en el material, tales como
tracción, deformación en frío, soldaduras, etc., ante la presencia de agentes químicos, principalmente compuestos clorados. Este tipo de corrosión se manifiesta por pequeñas fisuras en las zonas expuestas a tensión. Algunos métodos para prevenir la corrosión bajo tensiones son: selección apropiada del material, remover la especie química que promueve el agrietamiento, cambiar el proceso de fabricación o diseñar adecuadamente para reducir las tensiones.
CORROSIÓN POR GRIETAS (CREVICE)
La corrosión por grietas ocurre en las aberturas o los espacios estrechos entre dos superficies del
metal o entre superficies de metales y no metales. La aireación diferenciada entre la grieta (microambiente) y la superficie externa da a la grieta un carácter anódico. Esto puede contribuir a una condición altamente corrosiva en la grieta. Algunos ejemplos de grietas se forman en rebordes, arandelas, juntas, empalmes roscados y anillos. Algunos métodos para reducir los efectos de la corrosión de este tipo de corrosión son: eliminar la grieta en la etapa de diseño, seleccionar materiales más resistentes a este tipo de corrosión y reducir la agresividad del ambiente.
CORROSIÓN MARINA
La corrosión marina considera la inmersión de componentes en agua de mar, equipos y tuberías
que utilizan dicha agua, y corrosión en atmósferas marinas. La corrosión de un componente puede variar dependiendo de si está en una atmósfera marina, en una zona de salpicadura, o sumergido en el agua de mar. Además de la sal (NaCl), en agua de mar hay otros componentes como gases disueltos y organismos vivos. Las atmósferas marinas se consideran generalmente uno de los ambientes
más agresivos para la corrosión. Algunos factores que afectan la velocidad de corrosión en atmósferas marinas son: humedad, viento, temperatura, contaminantes aerotransportados, localización y organismos biológicos. La selección de la aleación, recubrimientos metálicos, recubrimientos orgánicos, y protección catódica son métodos de uso general para proporcionar protección apropiada a la corrosión. La protección catódica puede ser lograda usando un sistema de corrientes inducidas o impresas o un sistema de ánodo de sacrificio.
CORROSIÓN GENERALIZADA
de herrumbre en el acero. La vida de componentes se puede estimar en base a los resultados de pruebas de inmersión. Algunos métodos usados para prevenir o reducir la corrosión general son: recubrimientos, inhibidores, y protección catódica.
CORROSIÓN INTERGRANULAR

a temperaturas entre 430 a 870°C, estas temperaturas se presentan en las proximidades de
las zonas soldadas. Se forman carburos de cromo en los límites de los cristales de Austenita, empobreciendo la zona adyacente de este elemento (cromo) y quedando de esta forma expuesto a la corrosión. Una forma de evitar la corrosión intergranular es usar aceros de bajo contenido de carbono (tipo L), y cuando las condiciones de temperatura son aún más severas se debe usar aceros estabilizados. tipo de corrosión y reducir la agresividad del ambiente.
CORROSIÓN POR PICADURAS (PITTING)
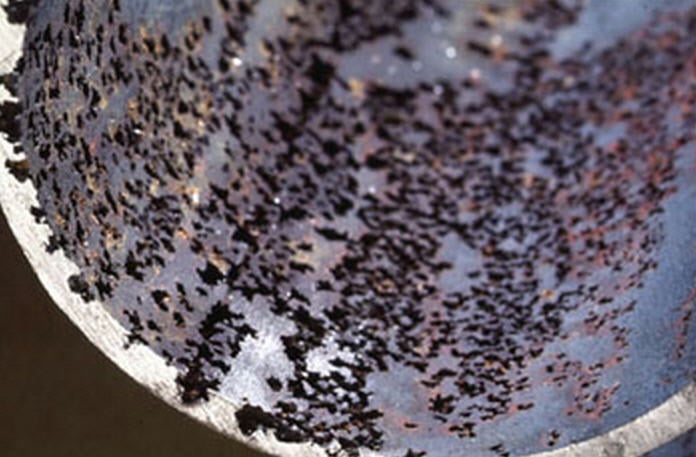
de agujeros en el metal. Estos agujeros pueden ser pequeños y difíciles de detectar visualmente
debido a la corrosión general. El pitting se asocia con discontinuidades localizadas del film de pasivación. La sensibilidad al pitting aumenta con condiciones extremas de agentes corrosivos, imperfecciones mecánicas, tales como partículas extrañas, daño en la superficie del material, o por fallas en la película de óxido de cromo. El fenómeno ocurre cuando se rompe la capa pasivante y hay un ataque muy localizado. Algunos métodos para reducir los efectos de la corrosión por picaduras
son: reducir la agresividad del ambiente y utilizar materiales resistentes a las picaduras. Es posible prevenir o retardar este efecto, usando aceros con contenido de Molibdeno, como el 316.
CORROSIÓN GALVÁNICA

Todos los aceros inoxidables son susceptibles a este tipo de corrosión. Se produce por el contacto de dos metales de distinto potencial de oxidación que están en contacto en un medio corrosivo. Como un metal altamente resistente a la corrosión, el acero inoxidable puede actuar como cátodo cuando está en contacto con material menos noble, generándose un fenómeno electrolítico que daña la superficie del acero inoxidable.
CORROSIÓN BAJO TENSIÓN
(STRESS CORROSIÓN CRACKING, SCC)
sin deformación significativa o el deterioro visible del componente. La soldadura genera gradientes de temperatura y así puede inducir tensiones residuales, lo cual en ciertos ambientes puede resultar en rotura por corrosión bajo tensiones. Este tipo de corrosión es el menos frecuente, se trata de un tipo de corrosión transgranular, el cual es producido por tensiones generadas en el material, tales como
tracción, deformación en frío, soldaduras, etc., ante la presencia de agentes químicos, principalmente compuestos clorados. Este tipo de corrosión se manifiesta por pequeñas fisuras en las zonas expuestas a tensión. Algunos métodos para prevenir la corrosión bajo tensiones son: selección apropiada del material, remover la especie química que promueve el agrietamiento, cambiar el proceso de fabricación o diseñar adecuadamente para reducir las tensiones.
CORROSIÓN POR GRIETAS (CREVICE)
metal o entre superficies de metales y no metales. La aireación diferenciada entre la grieta (microambiente) y la superficie externa da a la grieta un carácter anódico. Esto puede contribuir a una condición altamente corrosiva en la grieta. Algunos ejemplos de grietas se forman en rebordes, arandelas, juntas, empalmes roscados y anillos. Algunos métodos para reducir los efectos de la corrosión de este tipo de corrosión son: eliminar la grieta en la etapa de diseño, seleccionar materiales más resistentes a este tipo de corrosión y reducir la agresividad del ambiente.
CORROSIÓN MARINA

que utilizan dicha agua, y corrosión en atmósferas marinas. La corrosión de un componente puede variar dependiendo de si está en una atmósfera marina, en una zona de salpicadura, o sumergido en el agua de mar. Además de la sal (NaCl), en agua de mar hay otros componentes como gases disueltos y organismos vivos. Las atmósferas marinas se consideran generalmente uno de los ambientes
más agresivos para la corrosión. Algunos factores que afectan la velocidad de corrosión en atmósferas marinas son: humedad, viento, temperatura, contaminantes aerotransportados, localización y organismos biológicos. La selección de la aleación, recubrimientos metálicos, recubrimientos orgánicos, y protección catódica son métodos de uso general para proporcionar protección apropiada a la corrosión. La protección catódica puede ser lograda usando un sistema de corrientes inducidas o impresas o un sistema de ánodo de sacrificio.
Comentarios
Publicar un comentario